CNC machining trends in 2025 mark a turning point in the industry. In an increasingly demanding environment in terms of precision, speed and sustainability, the industry is embracing technologies that until recently seemed futuristic. From our experience as metal forming specialists, we introduce you to the innovations that are defining the new standard in advanced manufacturing.
1. Intelligent CNC machining trends: the evolution to autonomous systems
Among the most prominent CNC machining trends in 2025, the incorporation of artificial intelligence is undoubtedly one of the most transformative. CNC machining is leaving behind its role as a simple performer. Thanks to the integration of artificial intelligence and machine learning algorithms, today's machines are able to analyze data in real time, foresee anomalies before they occur and adapt their processes autonomously.
This advance has become one of the key pillars of the CNC machining trends, as it improves the quality of the final product, reduces tool wear, reduces downtime and optimizes energy consumption. It is, in short, a new era where efficiency no longer depends only on human skill, but also on machine intelligence.
This not only improves the quality of the final product, but also allows a significant reduction in tool wear, downtime and energy consumption. It is, in short, a new era where efficiency no longer depends only on human skill, but also on machine intelligence.
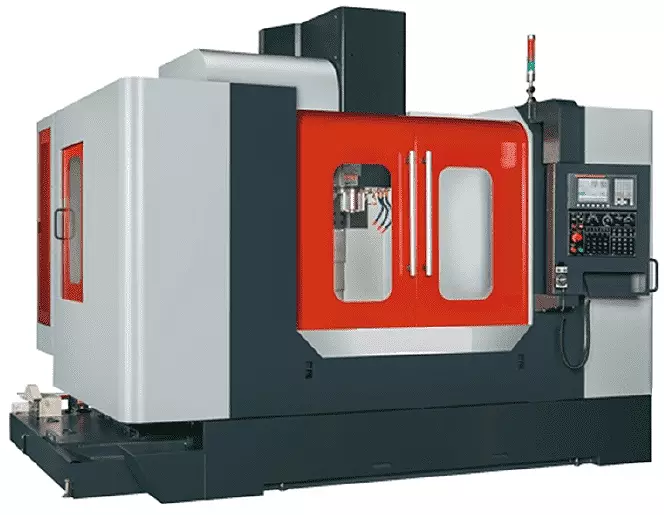
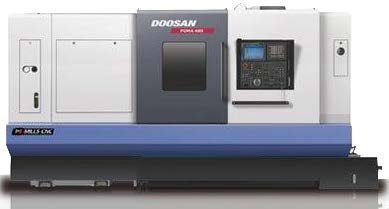
2. Collaborative robotics: CNC and cobots working in synch
Another major CNC machining trend that is revolutionizing the industry is collaborative robotics. Automation is not new, but the way it is evolving is. Collaborative robots - known as cobots - are no longer limited to basic tasks. Today they work side by side with CNCs, managing part loading and unloading, tool maintenance and even quality inspection tasks in real time.
This type of advanced automation aligns perfectly with current trends in CNC machining, as the cobots, equipped with machine vision, can identify defects during the process and enable their correction without stopping production. This reduces material waste and increases productivity without the need to expand the workforce.
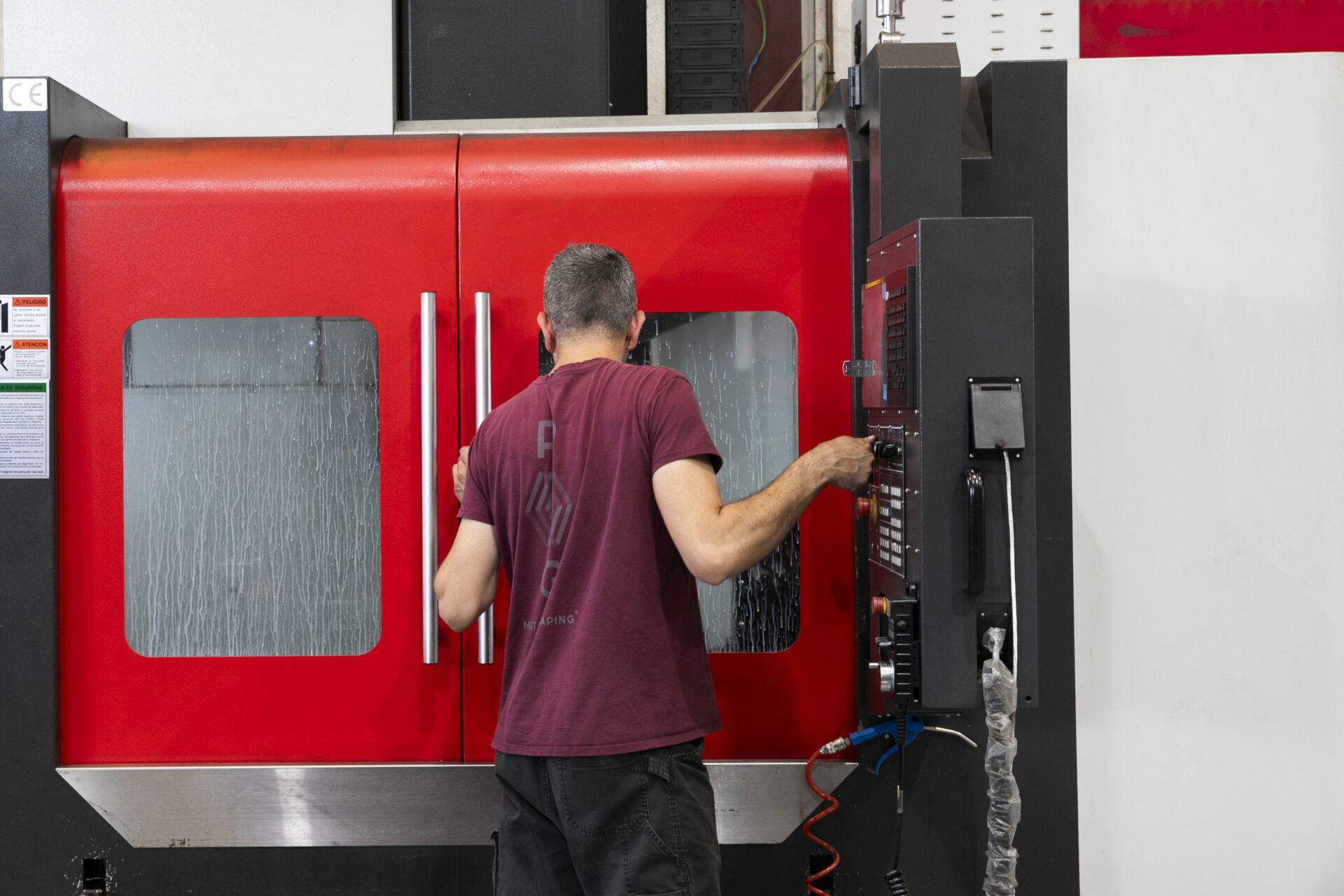
3. Hybrid manufacturing: when 3D printing meets CNC
Among the most innovative CNC machining trends, hybrid manufacturing is positioned as a disruptive solution. The boundary between additive manufacturing and conventional machining is blurring. By 2025, more and more machining centers will integrate 3D printing capabilities to create complex base shapes, which are then refined using CNC.
This hybrid approach, which is gaining more and more prominence within CNC machining trends, allows reducing production times, minimizing waste and creating geometries that were previously impossible with traditional methods. The result: functional prototypes ready in days, high-precision final parts and greater agility in the development phase.
This hybrid approach reduces time, minimizes waste and generates geometries impossible with traditional methods. The result: functional prototypes in days instead of weeks, and final parts with high-precision tolerances.
4. Trends in sustainable CNC machining: energy efficiency and lower environmental impact
Sustainability is also part of the CNC machining trends that are defining the future of the industry. The pressure to reduce the environmental footprint has reached the machining arena with a vengeance. New generations of machines are optimized to consume less energy, use environmentally friendly cutting fluids and make the most of every gram of raw material.
These sustainable practices, which are becoming increasingly common in CNC machining trends, are supported by intelligent monitoring systems that allow real-time parameter adjustment to avoid unnecessary consumption and extend tool life. In addition, the use of chip recycling and remote control of operations improve both the profitability and environmental impact of the shop floor.
Thanks to intelligent monitoring systems, it is possible to adjust parameters in real time to avoid unnecessary consumption and extend tool life. In addition, chip recycling and remote operation control systems are being implemented, improving both the sustainability and profitability of the workshops.
All of these innovations reflect how CNC machining trends are redefining both the processes and the mindset of the industry. It's no longer just about making parts with precision, but about making parts with speed, flexibility and lower impact.
Companies that know how to incorporate these technologies into their operations will be better positioned to respond to market demands, reduce costs and deliver greater value to their customers. Transformation is not optional: it is the new norm.
Do you need real CNC machining solutions for your project?
At R&G Metal Shaping we are committed to innovation in order to always offer the best to our customers. For this reason, we have recently incorporated the new Norma 45 Strapan advanced machining machine that allows us to successfully apply the main trends in CNC machining. Its high precision, power and capacity to work large parts help us to offer faster, more sustainable solutions adapted to every need. All this, with the support of an expert technical team, a modern infrastructure and a real commitment to quality in every project.
You can count on us to take your ideas to the next level.
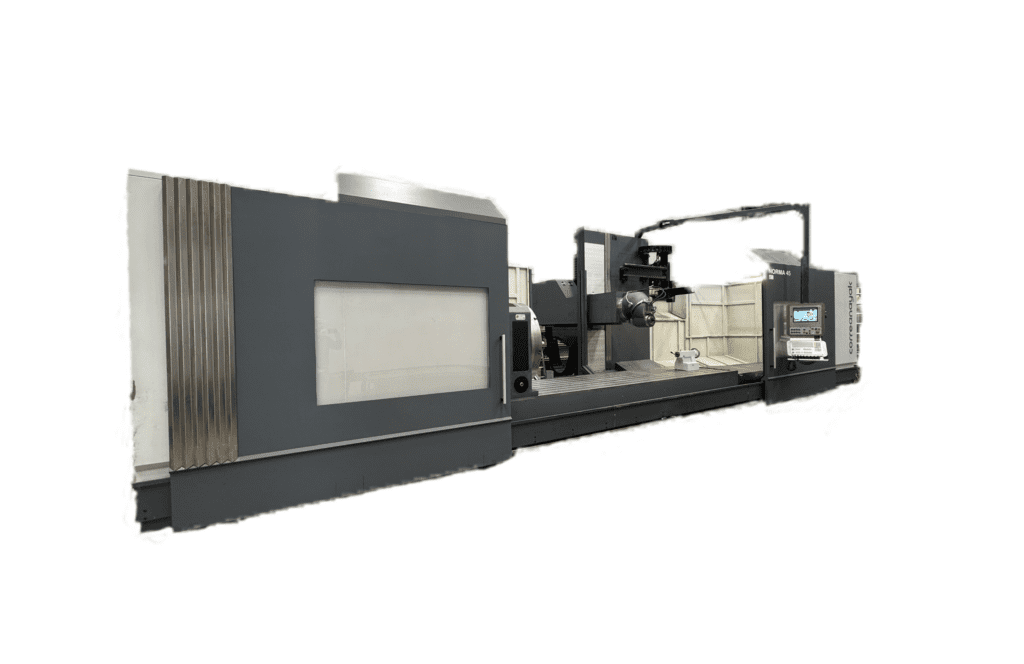